このブログをご覧になられている方の多くは、電気について興味・関心があり、さらには電験の資格取得を目指されているといった方では無いでしょうか?
また普段の仕事において、電気設備や工場機器の施設管理や保守・点検、工事監督をされている方もおられるかもしれません。
私自身はもともとは機械設計の出身であり、電気設備に関連する業務については全くのシロウトです。(スミマセン…)
実際、電気主任技術者の免状を取得した今日、現在においても、
『もし自分が将来、電気主任技術者として仕事をすることになったら、一体何をやるのだろう?』
と疑問と不安を感じております。
逆に、電気主任技術者として日々施設管理などの仕事をされてる方から見て、日ごろあまり馴染みのない機械設計・開発の仕事がどういったものなのか興味があったりするのでは?思い、自身の経験を元にまとめてみました。
- 就職(転職)に向けて電験の資格を取得して将来的には設備管理の仕事に就きたいが、設計・開発の仕事も興味がある。
- 普段から電気設備の保守、点検の業務に携わっているが設計・開発の仕事は実際はどんな感じなのか気になる。
といった方に是非読んでいただけると幸いです。
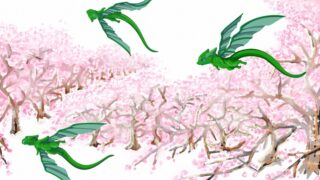
製品開発の流れについて
前職では精密機器メーカで一般消費者向けの機械製品、前々職では食品メーカで工場内の機械設備の設計をしていました。
一般消費者向けの機械製品としては、例えばカメラや時計、家電製品などを思い浮かべる方も多いでしょう。
より多くの人に使われ、普段から馴染み深いと思われる一般消費者向けの機械製品について、製品開発の大まかな流れについて説明していきます。
製品開発のフローチャート
製品開発の大まかな流れは下図のような感じで進んでいきます。
青枠は全体の流れ、オレンジ枠はその中にあって設計担当部門が主に関わるステップになります。
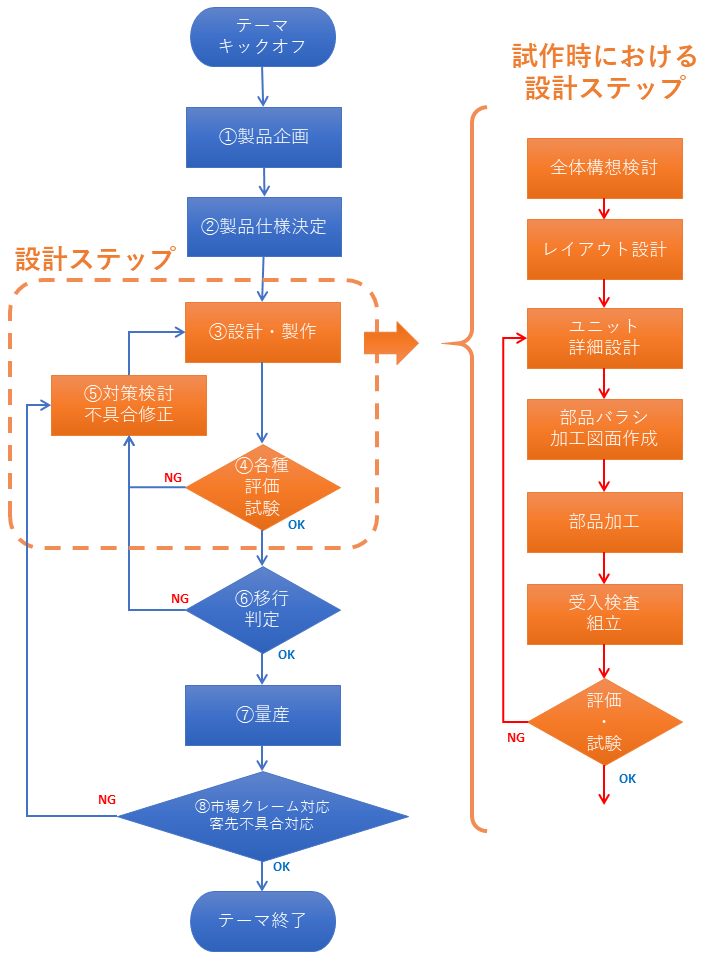
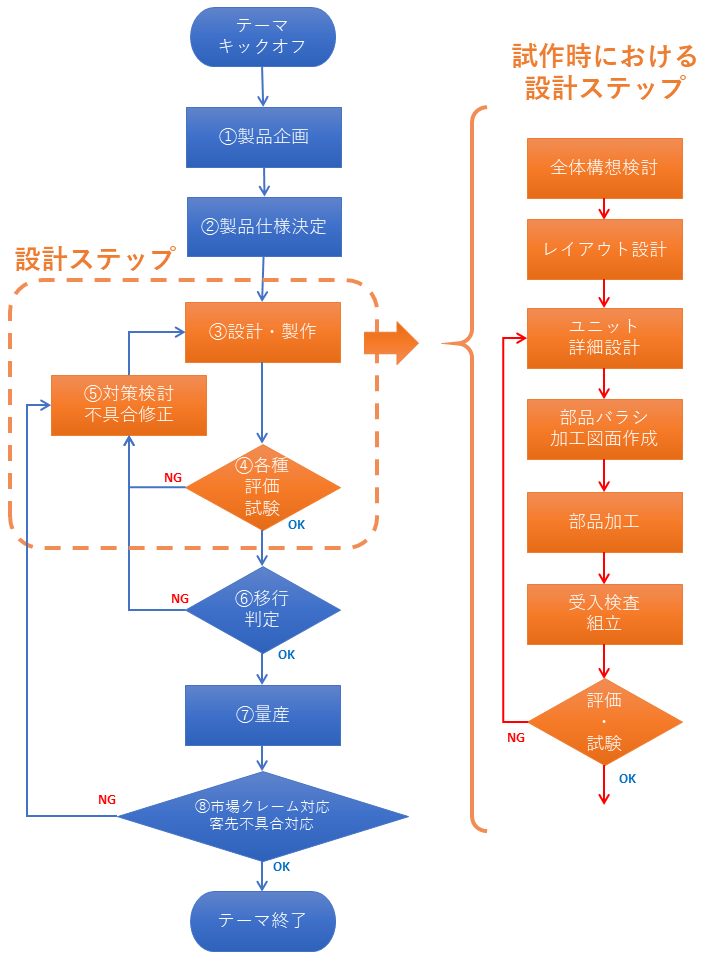
各ステップにおける具体的な実施内容
各ステップの項目について詳しく説明していきます。
- 企画担当から新製品の企画書が提出されます。最近の流行りやマーケティングによって得られた実際の使われ方、お客様の欲しがっている機能の調査、価格設定等がが出されます。
- 関連する各部門が集まって、製品仕様を決定します。例えば大きさや重量や仕入れコストや主な性能など。
- ここで決まった項目は後から変更するのは非常に大変なので、各部門とも、かなりピリピリした感じで進んでいきます。
- 製品仕様で決まった内容を実設計に落とし込むステップです。
- 全体構想構想検討⇒レイアウト設計⇒ユニット詳細設計⇒部品バラシ、加工図面作成と細かく設計を進めて行きます。
- 設計図面はCADを用いて行います。設計途中でCAEによるシミュレーションを用いて、強度解析や機構解析、構造解析を行うこともあります。
- 新製品へは新規技術の搭載が必須となり、他社製品による模倣を防ぐため、アイデアを整理して特許出願します。特許出願の件数は、通常業務における数値目標として設定され、なかなかアイデアが出ない場合は大変苦労します。
- 試作ステップの間は、設計者自身で受入れ検査、製品組立、評価試験を行うこともあります。
- 出来上がった試作機に対して品質評価、性能評価の他、加工性、組立性、安全性、サービス性などについても評価を行います。
- 評価、試験ステップで問題点や不具合を見過ごすと、市場に出てから大きなトラブルにつながってしまうので、第三者評価の際はかなり厳しいチェックが入ります。設計者にとってある意味“成績発表の場”といった感じでしょうか?
- 自信を持って設計した試作機であっても、周りから細かくアラ探しをされているような気分になりなかなか落ち着きません。
- コストについても目標コストをオーバしそうであれば、徹底的に見直しをかけて行きます。
- 各種評価、試験の結果NGであれば直ちに対策検討をし、不具合修正をしなければなりません。
- 評価、試験の結果がOKにならない限り、次のステップへ進むことが出来ず、開発テーマが中断してしまいます。
- 場合によっては期日を決められ、何としてもその日までに終わらせられるよう、連日徹夜といった事もありました。(働き方改革全盛の今日この頃ではあり得ないですが…)
- 対策検討、不具合修正を反映するためにコストや日数が多くかかってしまては意味がありません。最安且つ最短で解決することが必要です。
- ③設計・製作→④評価・試験→⑤対策検討、不具合修正のループが延々繰り返されないよう、常に最新の注意を払う事が必要です。(設計者にとって、最もつらい期間です)
- 設計ステップにおける問題点がほぼ解消され、残課題に対する目処が立った時点で、移行判定を行います。
- つまり、次のステップに進んでも良いかどうか(通常は量産化しても良いか)、関連する各部門の部門長も交えて審議します。
- 残課題が残っていたり、不具合を解消できる目処が明確になっていないと移行不可となり、後日再度審議を経ることになります。
- 残課題がすべて解消され、量産化判定が承認され、決裁されると晴れて量産です。
- 量産決定すると、ホントにホッとします。
- 量産化決定となると製品立ち上げに関わった人が集まっての打ち上げパーティーを開催したりしましたが、場合によっては一つの製品の立ち上げ数十人以上の人が関わることもあります。打ち上げパーティーの席で初めて見る人も多く、『あの人誰?』なんて事もしばしばありました。
- 量産後も市場クレームや客先不具合対応を行う場合もあります。(それほど多くは有りませんが)
- 量産後に問題がでると、リコールや市場機回収などのケースも出てくる場合もあり、悲惨な状況になります。(幸い、やっさんが設計した製品では市場問題はありませんでした…)
製品開発のサイクルは2~3年であり(2~3年おきに新製品の企画が立ち上る)、だいたいそのくらいの期間を経て開発テーマ終了となります。
リアルな機械設計技術者の日常
一つの製品を世の中に出すまでには、多くの人が関わってきます。実際の登場人物を見ていきましょう。
登場人物
設計担当のやっさんです。
色々悩みや苦労が絶えない設計者ですが、それなりにやりがいや面白みもあるんですよ。
自分の手掛けた製品が世の中に出たときは感無量です!
企画担当です。売れる製品は企画段階で全てが決まると言っても過言では無い!
市場のトレンドを見据えて、競合他社を脅かすような新製品の企画を提案します。
いわゆる新製品のプロデューサーだ。
カリスマ敏腕プロデューサーと呼ばれるよう、世の中の人をあっと驚かせる製品を世に出します!
やっさんと同じく設計担当です。やっさんとは別のユニットを担当しています。設計者同士で互いに協力しながらより良いモノづくりを目指します!
生産技術担当です。生産ラインを組んだり、生産計画を立てたりして、製品を低コストでタイムリーに世の中に出せるように頑張るゾ!
品質保証担当です。製品の良し悪しはまずは品質!試作段階から少しの不具合や不良も見落とさずに、しっかりとチェックするよ。
サービス担当です。お客様先でトラブルが起きたら、製品のダウンタイム(使えない時間)を少しでも短くできるように常に考えてるよ。
あとサービスパーツ(交換部品、消耗部品)は安くて、簡単に使えるようにして欲しいね。
調達・購買担当です。いわゆるコストの番人。仕入れコストや製造コストが1円でも安くできないか、無駄な費用がかかってないかしっかり見てくよ。
ある日の製品設計の一日
今度の新製品の企画書が出来上がったよ!
競合の『A社』のシェアを奪還するべく、A社製よりも10%コストダウンに価格設定。更にこれまで無かった新機能を盛り込みたい。
製品発売は、今年の夏ボーナスをターゲットに8月にプレス発表予定にしてるよ。みんなでいい製品を作ろう!
この製品は社長肝入りで、社運を賭けた新製品にすると経営TOPからのオーダーだ。みんなしっかり頼むぞ!
こんな短納期で、しかもコストもそうとう削られてるやん。
新機能追加とか、どうすりゃいいの??
取り敢えず試作機の初号機が完成!
よし!やっと試作機が上がったぞ。どれどれ、設計ミスは大丈夫かな???
やっさんの設計したところ、ウチのユニットにぶつかってるよ!もう少し小さく直しといて!
やっさんさぁ、これ組めないよ。どうやって部品付けるのよ?やっさんの所のユニットのせいで、生産ラインストップしてるよ~!早く直して~!
仕様書で決められた性能がちゃんと出てないよ。早く直して~!
部品交換がめちゃ大変ですやん。お客様先だと時間無いんだからもっと簡単に付け替えできるようにしてよ!
目標コスト大幅オーバしとるやん。要らない部品削るか、安い材料で同じ性能が出るよう設計し直して!
忙しいところ申し訳ない!お客様からの強い要望を今回の新製品に反映することになり、急遽、製品仕様が変更することに決定しました。大変だけど設計に反映してね。ヨロシク~!
やっさん、お前これホンマにちゃんと終わるんか?お前の担当のユニット、かなり遅れてるぞ!8月量産死守やからな!
あぁぁぁぁ~!!
とまぁ、こんな感じで設計者はいろんなところからさんざんとやり玉に挙げられて大変なのです…
しかしながら、このようなやりとりを何度となくも繰り返した暁に、最後の最後で自分の手掛けた製品がに量産され世の中に販売されるとなると、グッとこみあげてくるものがあります。
自分が担当した製品がテレビCMで流れた時は、思わず食い入るようにテレビにかじりついて見ましたね。
“機械設計者”あるあるについて
“機械設計職”をやって良かったこと
色々な人と仕事が出来る
製品を設計して世の中に出すとことは、色々な人と一緒に仕事をすると言うことに他なりません。
仕事を進めていく中でお互い自身の主張を譲らずに度々議論になったりしても、同じ目標に向けて一緒に頑張ってるうちに、結果として認め合い信頼できる関係になる事も多くあります。
もう、前職を退職してからはずいぶんと時間が経ってしまいましたが、当時一緒の製品の立上げに関わった人の中には未だに連絡を取りあう仲間も出来ました。
幅広い知識が身につく
一つの製品を設計して立ち上げていく上で、自分の担当している部分だけでなく周辺領域への理解や技術が身に付きます。
私の本職は機械設計ですが、モータ、センサー、ヒータなどの電気部品や素子を扱うことも多くありました。
非電気系出身でありながら、電気関連の知識を身に付けることが出来たのは、機械設計の仕事によるところが大きいと感じます。
電験の試験勉強に対しても、過去の設計経験が活かされた部分も多くあったと感じます。
やりがい、達成感を得る事が出来る
詰まる所これに尽きるのかもしれませんが、やはり自分の手がけた製品が世の中に出ると、感激もひとしおです。
設計者として経験を積んで行くうちに、単なる製品内部の一部品だけしか見てなかったのが、そのうち製品全体を見る事が出来るようになり、結果、自身の携わった製品への思い入れもより一層深いものとなります。
『あれ、俺が作った製品!』と言えるのも、設計者ならではだと思います。
“機械設計職”をやって大変だったこと
責任が重大
自身の設計が上手く行けばこの上ないですが、失敗するとすべての責任は設計者にかかってきます。
(場合によっては設計者の図面を承認した、その上司にも責任を問われることになります。)
市場で不具合が出ようものなら、それこそ『設計者出て来いや~!』と言われても仕方がありません。
設計者は常に失敗が無いか、ミスが無いかに最新の注意を払う必要があり、相当タフさが求められます。
品質・コスト・納期に常に追われる
いわゆる、Q(Quality:品質)、C(Cost:コスト)、D(Delivery:納期)になりますが、このQ・C・Dの呪縛からは逃れられません。
- 性能を出すために複雑な機構を搭載したが、設計に時間がかかって納期が間に合わない
- 安い部品を使ってコストダウンしたけど性能が出なくなった
といった事は許されません。
同時に、Q・C・Dは製品仕様で最初から決まっている事が多く、あとから変える事は決して許されません。
設計者は、テーマ終了まで常に品質・コスト・納期の事を最優先して意識することが求められます。
体力勝負
このように、責任重大で且つ、おちおち気も抜けない設計の仕事は、まさに体力が必須です。
若い頃、徹夜も苦にならない頃であればまだしも、年を取ってからも第一線で設計を続けている人は本当に凄いと思います。
私の前職では、設計の第一線で活躍された方の多くは40歳を越えたあたりから、プロジェクトリーダーや管理職になったり、あるいは品質保証部署やサービス部署に部署異動したりして、徐々に設計からフェードアウトされる方が多かったでした。
『生涯、現役の設計者』といった方は、本当に設計が好きでバイタリティに溢れた人なのだと思います。
機械設計の仕事は大変ですが、やりがいもあります。しかしながら、年を取るにつれて体力的にも厳しくなります。設計職を長く続けるのは大変ですね。
まとめ
“機械設計職”をやって良かったこと
- 色々な人と仕事が出来る
- 幅広い知識が身につく
- やりがい、達成感を得る事が出来る
“機械設計職”をやって大変だったこと
- 責任が重大
- 品質・コスト・納期に常に追われる
- 体力勝負
今回はここまでとさせて頂きます。
最後まで読んで頂き、ありがとうございました。